Printing inks ( Solvent Based ) for Glass
Inks Made in Germany
Printing on Glass:
Most of the organic inks for Glass are 2K (two-part reaction) inks and require post heating process. However in summers most inks are easier to use. In winters/Rain season a typical problem is of dew or moisture formation on the surface of glass poses a problem of adhesion. Hence the ink system must be able to work in summer and winter.The natural surface tension of some glass doesn’t allow quick bonding thus arising the need of adhesion promoters.
Printing on Glass is a very difficult subject especially with solvent based organic ink systems. RUCOINX has a very successful program for this since last 30 years.
RUCOINX are free from heavy metals are dish washer safe and chemical resistant. Inks can be applied either by Screen Printing, Pad Printing,Spray Coating or Roller Coating.
EPOXY and PU based ink systems work best on glass.
Solvent Based Solutions
Screen/Pad
Resistances:
- Alcohol
- Acetone
- Household cleaners
- Greases, oil
- Hydraulic oils
- Kerosene
- Petrol
Characteristics:
- Glossy
- Mat
- Tactile
- Foil Overprint
- Physically drying and chemically cross-linking through hardening additive
- Excellent mechanical and chemical resistance as well as high elasticity
- Lightfast and weatherproof
Applications:
- Cosmetics
- Houseware

RUCOINX T01 Series: Made in Germany
This glossy, physically drying, chemically reactive pad &screen-printing ink exhibits good mechanical and chemical resistance, as well as a good flexibility. The colour shades of series T01 are light fast, weather resistant and guarantee high opacity. Higher temperature 150°c-180°c for 30 minutes gives very good dishwashing and chemical resistance.
Series | Hardener 100VR1294 | Drying Time | Adhesion Levels | Chemical resistance level |
T01 | 2% - 10% | 150°c-180°cx30min. | 9 | 9 |
Ink Type:Two-part reaction
Substrate: Glass, acrylic glass, lacquered surfaces, metal, thermosets, PE PP
Finish: High Gloss
Mixing Ratio: Add hardener (100VR1294) to the main agent at the ratio at 1:10 and agitate them well before use. Use with in the pot life 6-8 hours after which the mixture will turn to gel or lose its designed physical properties.
Diluent: Use the following solvents (15:25% weight) to adjust viscosity: standard solvent (38571), fast dry (35353) and for Glass (100VR1390), retarder for screen printing 34392,35696
Drying Time: Natural and Thermal curing. Sets to touch in 5 minutes at room temperature at 21°c. While adding hardener to the ink, drying of the ink will take approximately 36 hours at room temperature. To accelerate the ink drying onto the substrate the use of hot air blower or infrared lamps is recommended. Heat treatment at 150°c for 30 minutes is recommended for the best result.
Applications
- Cosmetic containers like bottles of perfume and oil.
(T 28,110GE, T-01)
- Touch Panels, Capacitive Touch Panels of electronic devices.
(T-01 HF)
- Acid wash effect ink and coating
RUCOINX have an interesting organic ink solution to replace the toxic and dangerous acid etch which is done by Hydrogen Fluoride Acid (HF acid). Applications are done by spray coating or screen printing.
- Over foiling or Inline foiling
A special inline screen-printing ink is screen printed followed by foiling only on the screen-printed surface.

RUCOINX T28 Series: Made in Germany
Many users do not have facility to post heat glass for a long time so T28 is made for such applications where curing speed is fast. Heating required is 120°C just for 10 minutes. However, the adhesion level is improved with passage of 72 hours.
Caution: Higher temperature than (120°C) makes the ink matt.
Series | Hardener 100VR1294 | Drying Time | Adhesion Levels | Chemical resistance level |
T28 | 2% - 10% | 120°cx20min. | 8 | 8 |
Ink Type:Two-part reaction
Substrate: Glass &ceramics and metal
Finish: High Gloss
Mixing Ratio: Add hardener (100VR1294) to the main agent at the ratio at 1:10 and agitate them well before use. Use with in the pot life 6-8 hours after which the mixture will turn to gel or lose its designed physical properties.
Diluent: Use the following solvents (15:25% weight) to adjust viscosity: standard solvent (38571), fast dry (35353) and for Glass (100VR1390), retarder for screen printing 34392,35696
Drying Time: Natural and Thermal curing. Sets to touch in 5 minutes at room temperature 21°c. While adding hardener to the ink, drying of the ink will take approximately 36 hours at room temperature. To accelerate the ink drying onto the substrate the use of hot air blower or infrared lamps is recommended. Heat treatment at 120°c for 20 minutes is recommended for the best result.
Applications of T-28 inks
- Glass decoration, cosmetic industry

RUCOINX 110GE Series: Made in Germany
110GE is a heat set screen printing ink. Final oven curing is a must for this ink. This ink is weather resistant, dishwashing safe and very hard ink. Curing temperature is 180°C for 30minutes.
Series | Hardener 100VR1294 | Drying Time | Adhesion Levels | Chemical resistance level |
110GE | 2% - 10% | 150-180°cx20-30min. | 10 | 10 |
Ink Type:Two-part reaction
Substrate: Glass &Ceramics
Finish: High Gloss
Mixing Ratio: Add hardener (100VR1294) to the main agent at the ratio at 1:10 and agitate them well before use. Use with in the pot life 6-8 hours after which the mixture will turn to gel or lose its designed physical properties.
Diluent: Use the following solvents (15:25% weight) to adjust viscosity: standard solvent (38571), fast dry (35353) and for Glass (100VR1390)retarder for screen printing 34392,35696
Drying Time: Only thermal curing. Sets to touch in 40 minutes at room temperature 21°c. To cure the ink drying onto the substrate the use of hot air blower or infrared lamps is recommended. Heat treatment at 180°c for 30 minutes is recommended for the best result.
Applications of Series 110GE
- Glass decoration, promotional items
- Decoration of glass, ceramic and metal
Disclaimer: Substrates may differ in their chemical structure or method of manufacture. A test for suitability must always be carried out before printing.
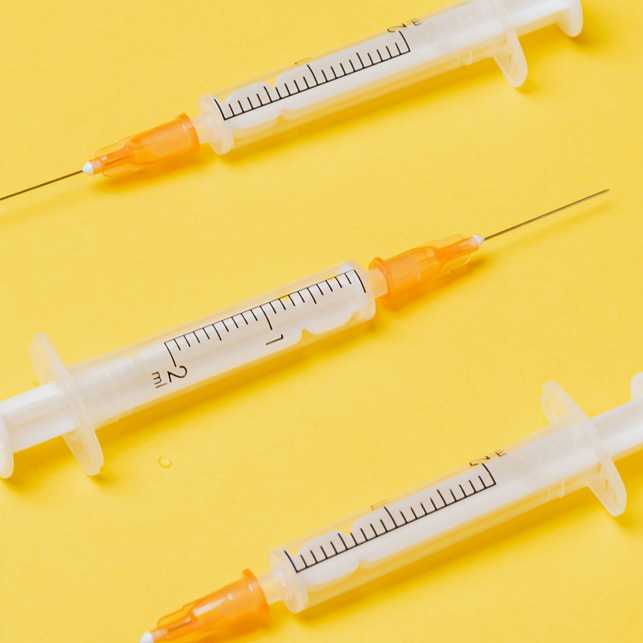
Non-toxic Printing Inks and Pad Printing machine for Printing on Disposable Syringe
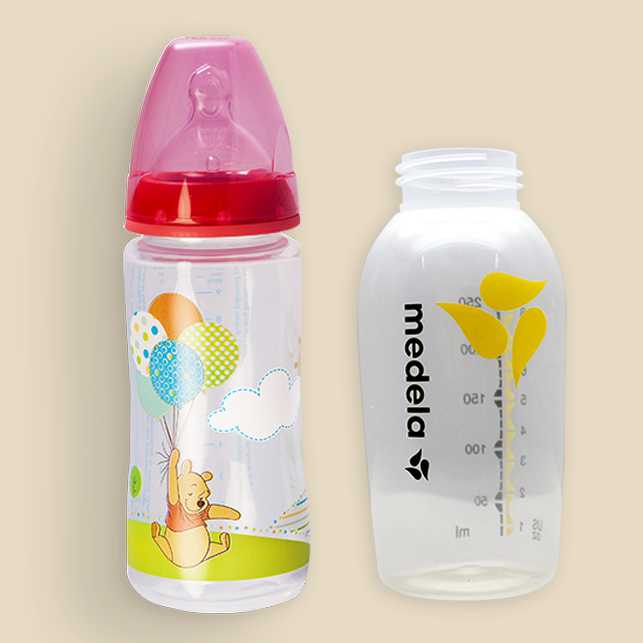
Printing Solutions for Feeding Bottles
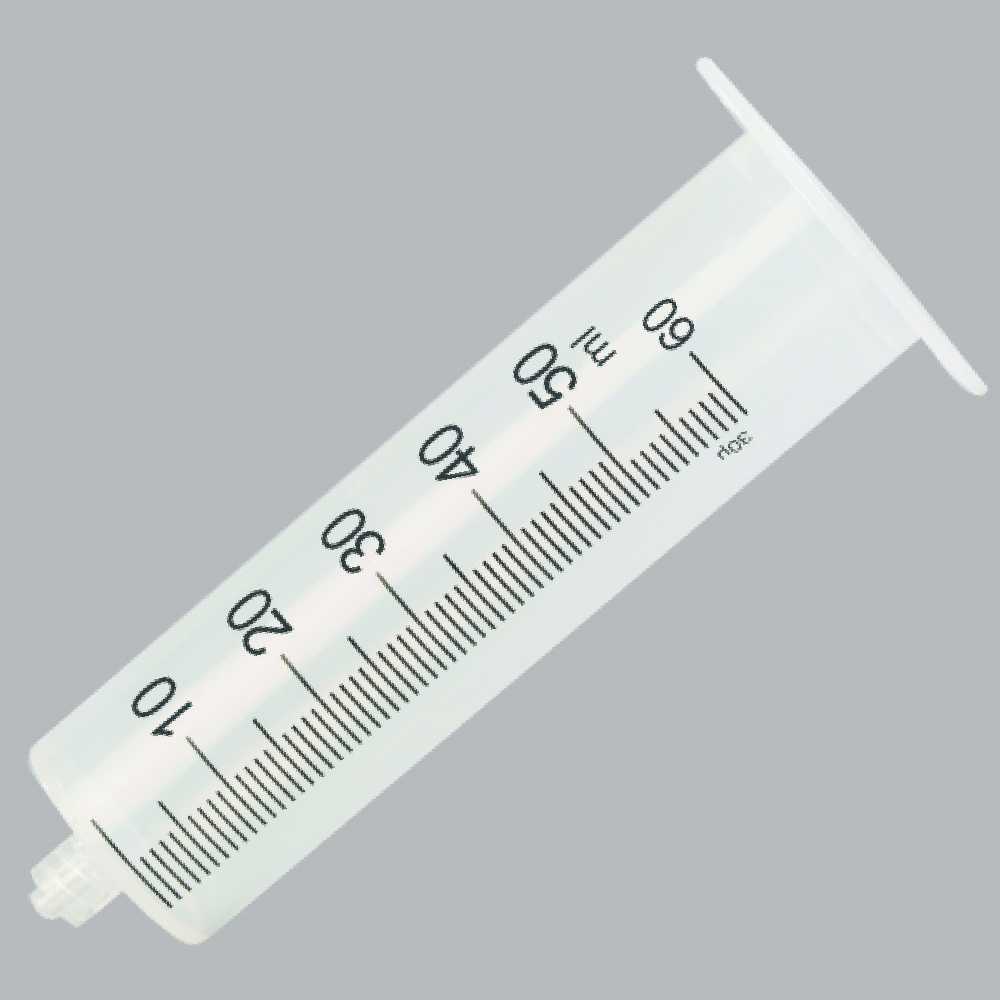
Printing of Medical Ampoule Strips: Machines & Inks
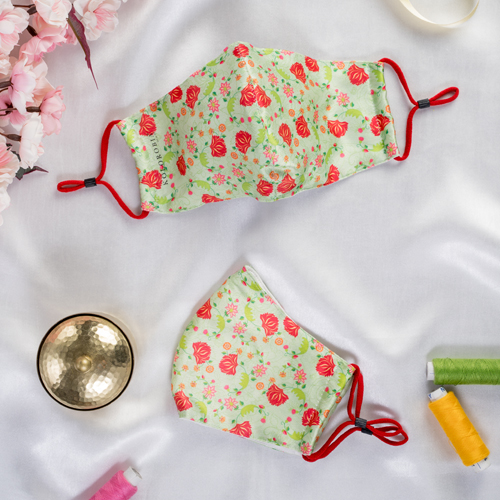
Face Mask Tagless Printing Solutions
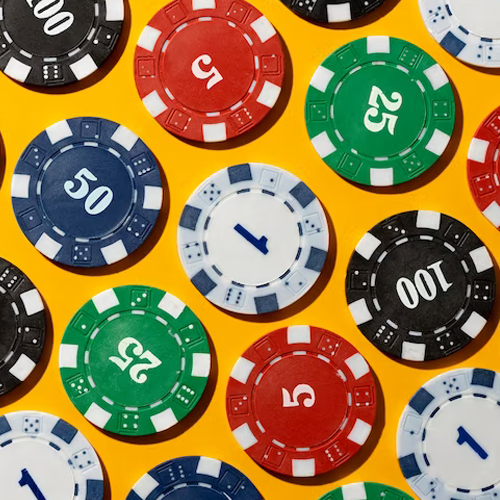